A simple yet effective way to standardize operational processes across your operation is by incorporating the use of forms and checklists. From opening and closing tasks to proper hygiene and food storage, a form or checklist can reduce labor costs, minimize waste, strengthen business performance, and increase customer satisfaction. It also helps prioritize employee functions and even achieve legal compliance with food safety standards.
Because every foodservice operation performs a thousand different tasks every single day, relying on a super extensive form or checklist has the potential to be counterproductive. Instead, food operation spec sheets should be broken up into categories with different forms assigned to the respective departments within the operational setting. Doing this will allow employees to be more efficient and accurate when completing the forms.
The information you gather from these forms can help each operation identify improper food handling and preparation practices, poor personal hygiene, unsanitized equipment, and generally help root out unsatisfactory practices. It will also give staff the opportunity to correct any tasks or processes as they work through the list to ensure that the operational standards are met and maintained.
The most important consideration when using operational checklists is whether the items on your forms are asking the right questions. We’ve identified four key elements to ensure your checklists are effective and can be used to streamline your operation. Paired with the right tech tools, these checklists can be seamlessly integrated into daily procedures, generating real-time feedback and automated alerts that will minimize waste, reduce costs, increase operational performance, and provide real-time insights.
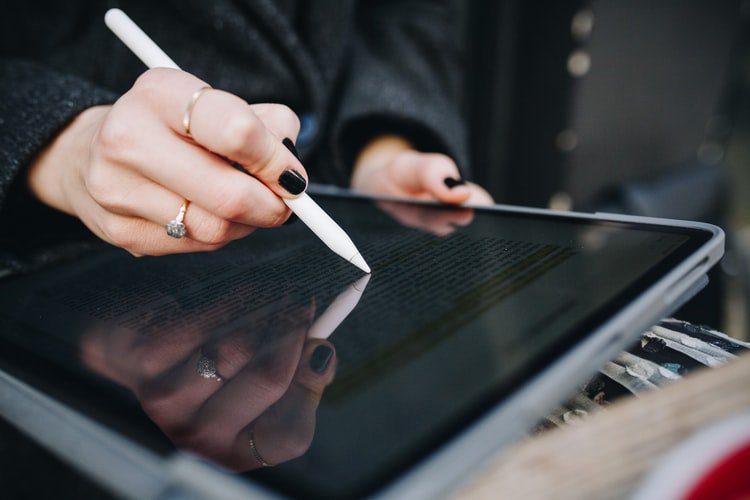
Four Key Elements to Creating Effective Operational Forms and Checklists
1. Be Focused
Before you create your checklist, you must first determine what it serves to accomplish. Knowing what kind of data you need to collect and what you want your employees to do will inform your questions. If you are building multiple forms, you and your team need to understand the value of each of them.
Example: One of many goals is to reduce food waste. To determine the amount of food discarded due to expiration and spoilage, the form includes a list of all the types of fresh produce used. Respective employees on duty are required to weigh and document quantities being discarded at the beginning or end of each day. The form will have space for employees to fill in the exact quantity or weight discarded (e.g., 5 lb butter lettuce) and note how much of the item is in stock.
This allows the kitchen manager or operational staff to assess where too much fresh produce is being ordered and reduce food waste, food expenses, and identify possible flaws in the storage conditions of perishable items.
2. Be Quantitative
Don’t leave any room for subjective interpretation of facts. The best type of question is specific and requires yes/no answers, multiple-choice, or exact numbers. This ensures that the information gathered is standardized and concrete. It also makes it easier and quicker to complete the checklist. There will be little room for misinterpretation if someone new is completing the questionnaire on a certain shift or as a stand-in.
Example: Consider the same scenario where staff documented the fresh produce that was discarded. The questionnaire could have been, “Is there enough butter lettuce in stock?” This type of questioning is open to interpretation depending on who was on duty. Instead, specific information was required. A more effective question would have been: How much was lettuce was thrown away? How much was in stock? This data allows for effective data-driven decision-making about ordering and storage.
3. Be Qualitative
The best way to do this is with photos combined with quantitative information. Quantitative questions should be used for the hard facts, while qualitative information backs up those facts. Using images offers immediate context and saves time writing out long descriptions, and avoids misunderstandings. Using mobile apps for audits and checklists allows users to easily complete the digital forms, take photos on their phone or from a company iPad or tablet and attach them automatically with the checklist submission.
Example: A form can require that a question about kitchen equipment cleanliness is accompanied by a photo. This way, management can actually verify what the kitchen equipment looks like without actually being there.
4. Be Concise
Forms that are easy to complete will not only take up less time for employees to submit but will also be focused, resulting in a clear and concise view of the status of the store. Checklists should be completed and submitted at predetermined intervals depending on the specific department's needs.
Example: Teams can pick up trends based on weekly operational data. If high butter lettuce wastage amounts are continuously recorded, then the team can consider reducing order quantities or adjusting storage conditions to minimize waste.
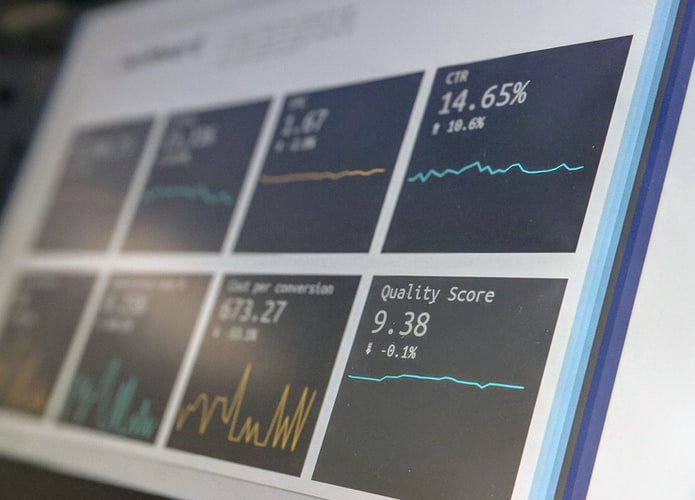
Integrating Tech for Maximum Success
It is impossible for managers to be at every store all the time. Food safety checklists and audits are used to ensure that adequate storage, food handling, hygiene, cleanliness, and operational service standards are met, whether management is there or not. Additionally, operational checklists can help decrease expenses, assist in data-driven decision-making, and reduce the risk of fines or harm to brand reputation.
Zenput’s digital checklist can be seamlessly integrated into your operation to streamline food safety and operational functions. The app allows employees to capture photo evidence, annotate them, and attach them to digital forms for a comprehensive view of the store.
The features of Zenput include:
- Automated notifications when tasks are not completed or properly executed. This helps hold employees accountable and ensure issues are addressed.
- The automation of corrective measures assigned to the relevant staff with due dates, stated priority levels, and feedback.
- A scheduling feature for inspections and audits to be submitted with real-time reports where management can immediately see data regardless.
With the generation of real-time operational reports and analytical features, managers can gain performance visibility and insights on productivity and compliance. Simplify your operation with streamlined audits and checklists by booking a Zenput demo today.
Subscribe to our blog
You are now subscribed!